Split Wood Fruit Basket
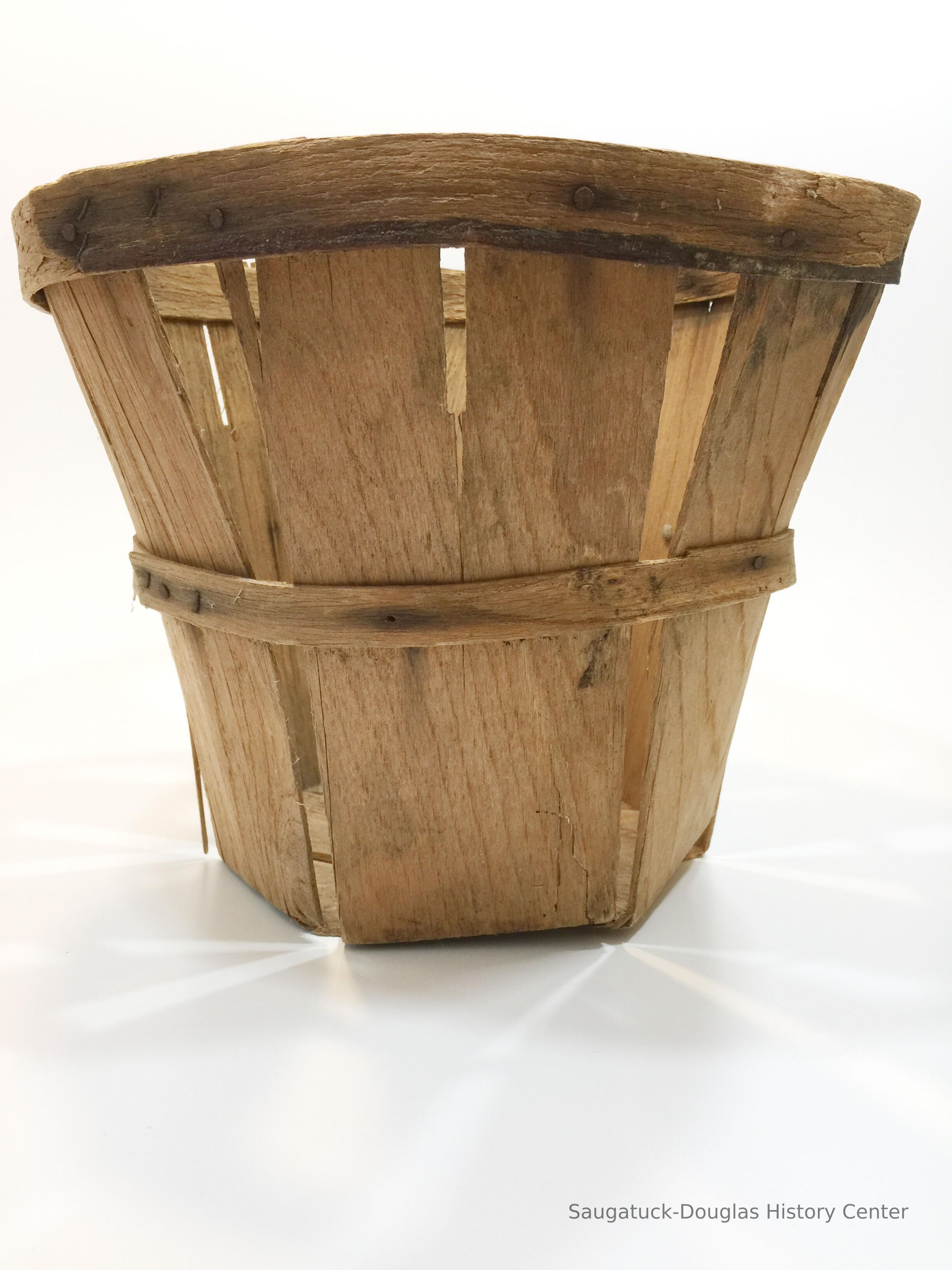
2021.67.07
Industry and manufacturing1875 Basket factories
Winthers, Sally
Width is 10 inches at rim, 6 inches at base
9 in
10 in
Sec 2E Shelf S21
https://sdhistoricalsociety.org/publications/NLHist/NLHist/P398-401.php The Douglas Basket Factory By Retha Haan (In the early 1960s Douglas resident and teacher, Retha Haan, interviewed Mrs. Elmer E. Weed, Mrs. J. Everett Durham, William Devine, Fred Schultz and Mrs. Wallace Williams and wrote this synopsis of a Douglas factory.) In Douglas, Michigan, back in the 1870s when the lumbering, tanning and boatbuilding industries which had made it a busy and thriving little village, were beginning to wane and the "Peach Era" was beginning to boom in southwestern Michigan, Captain Robert Reed, who had a large fruit farm on the shore of Lake Michigan at Douglas, started and operated a small basket factory at the foot of Tannery Hill on the Kalamazoo River. The operation was later moved to a new location, on a bend of the river, on the north side of Douglas. In 1 872 it was sold to William and Joshua Weed who enlarged it and it was called the "William Weed and Company Basket Factory." The first fruit package which the Weeds manufactured from a patent which they invented was known as the Wobble Crate, so called because of the crossed pieces, or wobble in the bottom of the square crate; which kept the four round, peck peach baskets in position in the crate. The baskets were made from veneer splints, nailed to a solid bottom and were kept in shape and made firm by hoops nailed around the top, center and bottom of the basket. Later, Joe Devine and Everett Durham invented a machine for sewing the hoops to the basket, in one operation with wire. This was a big money saver as it had cost 50 cents per hundred to nail hoops; but they could be sewed for 17 cents per hundred. Berry boxes and crates were also made. The boxes were made from two pieces of scored veneer. The scoring enabled the veneer to bend, shaping the box. At first they were nailed together, but later, probably after 1900, they also were sewed with wire. The first sewing machines were foot-operated, but later ones were power-operated. The first Climax baskets, which we know as grape baskets, were made by the Dickey factory in Douglas, which early went out of business and their machinery was moved to Cadillac. Later Climax baskets, in 5th and 6th bushel sizes were also manufactured in the Weed Basket Factory. One informant asserts that Roger Reed of Douglas made the patent for the bushel basket. Another asserts that he and Everett Durham invented the form far making the Jumbo basket, although they never received any financial benefit from their invention. Be that as it may, the factory did manufacture all of these types of baskets and berry crates and boxes, becoming one of the largest fruit package manufacturing plants in Michigan. During later years the local firm was connected with a factory in Lawton, supplying the baskets for the large Lawton and Paw Paw grape vineyards. When William Weed's son, Elmer, finished college, William turned his interest in the factory over to him and it was renamed "E. E. Weed and Company." About 1896, Frank Kirby, who was bookkeeper for the factory and also held an interest, died, and D. Milton Gerber took over his interest. James Wark also came in and a stock company was formed. William Tisdale and Everett Durham held working interests. When the stock company was formed the name of the factory was changed for the last time to "The Douglas Basket Factory." After 18 years in the factory, Elmer Weed withdrew and Mrs. Kirby took over some of his interest; although he continued to hold stock in the company until the factory burned. Mr. Work managed the plant for some years; then he became ill and William Devine took over Mr. Work's work as manager and was given $2,000 in stock. When the factory was owned by the Weeds, it never had a very reliable financial status. It required quite a lot of capital to operate and there was not much to be had. The work, because of its nature, was necessarily seasonal. A man earned about $1.50 per day for day labor. Piece workers could sometimes earn $3 or more per day. A single man received $5 of his wages each week in cash; a married man received $b. The workers were then given an order on the grocery store for the rest of their wages, which was paid up when the company collected for baskets at the end of the season. After Gerber and Wark took over, the factory was on a sound financial basis and workers received the entire amount of their wages by check each week. In the early days of the factory, when the baskets and crates had to be nailed by hand, nailing was considered a trade and 10 or 15 nailers were imported for the summer. They were rather rough individuals, heavy drinkers, and they followed the crop from place to place, very much the same as tramp coopers. They began about May 1 and worked until about October 1. About 25 or 30 women also worked at nailing. The factory continued to expand. About the time that Gerber and Wark became interested in the factory, they realized that the supply of local timber was nearly exhausted, so they bought 2,500 acres of timber along Swan Creek, near Allegan, and 2,500 acres along the Kalamazoo River. The logs were cut and piled on the banks of the Kalamazoo River in winter and floated and rafted to Douglas in spring and summer as needed. A raft of logs was on its way down the river when the factory burned. The work of cutting, trimming and scaling the lags, cutting the limbs into cordwood and piling same, kept a crew of 25 to 30 farmers and Indians busy in winter. Some of them then worked in the factory in the summer. The men received $2 per 1,000 feet for cutting logs and $1 per cord for 18-inch hardwood. The Indians and farmers did a good job. they felled and cut the logs to good advantage and cut and piled the wood honestly and straight. Beech and maple were used mostly for staves, elm for hoops, basswood and whitewood for berry boxes and soft maple was best for slats and covers for berry crates. The logs were sorted as to use before floating down the river. They were steamed after reaching the factory and then the veneer was cut round and round until all that was left of a log was a pole about four inches in diameter. The veneer was also scored, by the veneering machine, so it would bend and then cut into the desired size sheets. During the "Peach Era" the factory was making more than a million Climax baskets a year, with bushels and crates in proportion. Lake boats made daily trips to Chicago carrying peaches from Douglas, Pier Cove and South Haven. Farmers with loads of peaches were often lined up at the piers for blocks, waiting to unload onto the boats. These same farmers took home loads of empty baskets from Douglas. The factory gave employment to 100 to 300 people depending on the fruit crop. Production was divided into department. Mr. Everett Durham was in charge of basket manufacturing and Harry Forrester had a contract for making berry crates and boxes on commission. This last named department was now carried on in a building across the road from the main factory. However, it became increasingly expensive to operate the plant as it became larger. A filer, engineer and fireman were employed the year round. In order to hold help, baskets had to continue being made even though the fruit crop was scarce. Several large warehouses far storing the surplus were built which were filled to capacity when the factory burned on April b,1927. Thus ended the career of one of the many small enterprises which help to make great our villages, cities and nation.
11/02/2021
08/17/2024